
Case Study
Advantage Converting Reduces OEM’s Manufacturing Costs and Opens the Door to Further Innovation
Challenge
A major subcontractor for a multinational OEM produces RFI shields used in the manufacture of Magnet Resonance Imagining (MRI) machines. The shields are composed of copper and G10 (a rigid fiberglass laminate). The company was using an expensive waterjet process to cut the shields, and wanted to reduce its costs and scale production. However, at 36×50 inches, the size of the parts limited the type of manufacturing processes and the number of partners that could help.
Solution
The company’s search for a partner that could laminate and die cut multiple RFI shields led them to Advantage Converting. We have the capability to die cut up to 78 inches wide and can process rigid materials on our existing tooling and equipment.
Our engineers developed a more efficient and cost effective process that entailed laminating the copper foil and composite G10 using acrylic adhesive and then die cutting the shield on our large platon die cut presses. We adhered to the company’s whole dimensional tolerances, edge quality and other quality requirements.
Results
- The laminating and die cutting process we employed reduced the OEM’s manufacturing costs by 35% and improved customer lead times by three weeks
- We scaled production and improved yield
- Eliminating the challenges associated with the part’s size freed the customer’s engineers to further innovate and develop a second generation product that improved the overall efficiency of the end product
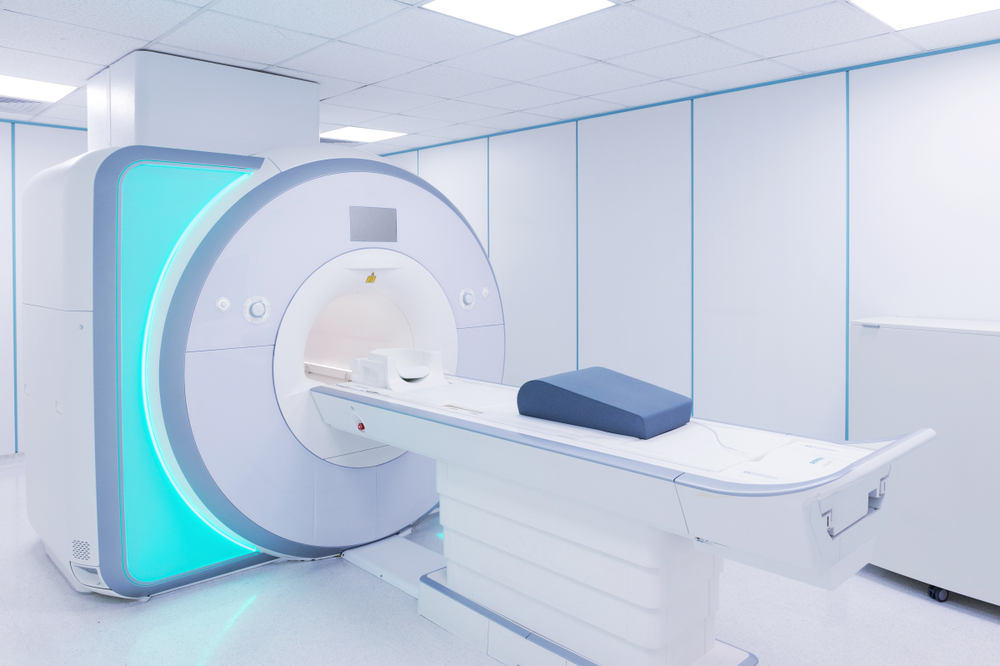